Ça faisait longtemps que je me disais qu’une presse à badges serait utile. Aussi bien pour préparer des goodies pour le stand et les salons que pour le FabLab. Une presse à badges permet de créer une activité avec des enfants, création de leur badges (dessin, respect de la norme pour les dimensions, consignes pour la fabrications…), et ils repartent avec leur création !
J’ai reçu ce produit gratuitement pour les tests, envoyé par Vevor. C’est donc un
============= Article sponsorisé =============
Vevor m’a offert le matériel et j’ai choisi de rédiger cet article,
tout en conservant ma liberté rédactionnelle.
Au sommaire :
Presse à badges VEVOR Ø44mm
Déballage
On reçoit une caisse en carton épais et… lourde. La caisse mesure environ 50x35x35cm. A l’ouverture, on trouve sous une plaque de mousse, le cutter rotatif réglable et deux gros sacs de la partie arrière des badges. Il y en a 1000… Ça tient de la place !
Chaque coupelle est munie d’une épingle qui permettra d’attacher le badge sur un vêtement.
Un ressort donne son élasticité à l’épingle.
Le cutter rotatif, c’est une lame de cutter qui est montée sur une coulisse réglable. D’après la documentation il faudra faire un cercle de 54mm. On verra ça un peu plus loin
Ensuite on a la coupelle métallique qui va supporte l’image et venir se serrer sur la partie arrière.
Finalement on a deux sachets contenant chacun 500 feuilles de plastique transparent qui seront la protection du badge.
La notice (en anglais) permet de démarrer même si on ne parle pas couramment anglais, elle est abondamment illustrée. Vous pouvez la télécharger en cliquant sur ce lien.
Dans une autre boîte en carton on va trouver les « moules » ou « empreintes » qui vont servir à former le badge. Ici pas de petite économie. On a des empreintes en inox massif lourd et costaud. Pas de danger que ça se déforme ! Ci-dessus c’est la partie supérieure, qui vient se placer dans la partie mobile de la presse. (poids ~500g)
Et ici ce sont les deux moules inférieurs. Celui de gauche recevra la coupelle en métal, alors que celui de droite sera juste garni avec la partie arrière. Une glissière en plastique épais permet de faire coulisser les deux moules à tour de rôle sous la presse. (poids 1,1Kg).
Dans une caisse qui était au fond de la grande caisse en carton on trouve la plaque de fond et la poignée.
Là non plus ça ne rigole pas ! la plaque est en métal épais. Ça pèse quand même presque 1,6Kg, cette chose !
La poignée n’a rien à envier à la plaque support. Elle est solide et réalisée en acier costaud (plus de 400g).
Un sachet contient les clés pour le montage de la presse et le réglage des moules. Plusieurs pions de blocage sont fournis pour la glissière.
Au fond de ce deuxième carton on trouve la partie « active », c’est le corps de la presse. La aussi c’est du lourd avec plus de 2Kg sur la balance. Une fois le tout monté on dépasse allègrement les 5Kg !
L’ensemble du matériel est sorti des cartons. Tout est en bon état, l’emballage est sérieux et n’a subi aucun dommage. On va pouvoir passer au montage.
Montage de la presse
J’ai commencé par mettre en place la poignée. Il suffit de la visser à fond dans le filetage prévu en haut de la presse. C’est un excentrique qui va appuyer sur le piston de la presse (je ne parle pas du gars qui tient la poignée, mais d’une pièce mécanique de la presse ! 😀 )
Positionnez ensuite la presse sur la plaque support.
Mettez les deux vis et les rondelles dans les trous du socle de la presse, et serrez avec la clé 6 pans.
On voit sous la plaque que les vis sont bien calibrées car rien ne dépasse. vous pouvez poser votre presse sur une table sans crainte. Par précaution, je mets quand même une protection sous la presse .
Mettez en place la partie supérieure de la presse. Il y a un cran sur l’axe et vous devrez tourner un peu pour trouver la bonne orientation.
Cette partie de la presse tient en place par aimantation. Poussez la vers le haut, elle va se solidariser à la partie haute de la presse.
La partie basse de ce moule est mobile, dans mon cas elle est redescendue seule après quelques secondes.
Mettez la glissière en place avec les deux moules. Un pion de blocage est déjà monté à droite, il vient en butée quand vous poussez suivant la flèche noire.
La partie basse du moule supérieur bloque la glissière. Soulevez la momentanément (flèche jaune) et poussez la glissière (flèche noire).
Prenez le pion de blocage dans le sachet de pièces (j’en ai trouvé 3 dans le sachet, on en a deux de secours 😛 )
Mettez le pion de blocage gauche en place. La presse est prête à être utilisée.
Caractéristiques
![]() |
![]() |
La presse à badge a des dimensions plutôt réduites et un poids de plus 5Kg, ce qui assure une bonne stabilité.
Utilisation
Le fonctionnement est simple et bien expliqué graphiquement.
Vous pouvez avec la même machine créer des badges mais aussi des décapsuleurs, des magnets, des miroirs.
La presse à badges est fabriqué à partir de matériaux de haute dureté. Le corps est en fonte avec une base lourde en métal qui la rend robuste et durable. L’utilisation est sûre et agréable.
La poignée de la machine à fabriquer les badges est conçue de façon ergonomique. Elle offre une prise en main confortable. Le caoutchouc antidérapant sur le haut de la poignée évite que la main ne glisse.
Les matrices en acier inoxydable sont interchangeables. Vous pouvez changer pour d’autres tailles si besoin. La glissière en plastique permet un positionnement précis et facilite le processus de fabrication de badges.
Ce genre de machine est souvent utilisé pour créer des badges faits maison pour des campagnes politiques ou des événements sportifs ou festifs.
Préparation du badge
Impression
D’après le tableau fourni avec la presse, pour un badge de 44mm, l’image peut mesurer 39mm et le cercle extérieur du papier découpé sera de 54mm.
Pour une utilisation avec le film plastique et du papier imprimé « maison » le papier maxi peut être compris entre 115 et 135g/m2.
SI vous utilisez du papier photo, son épaisseur doit être inférieure à 0,2mm.
Découpe
J’ai fait plusieurs essais bien entendu, avec du papier 80g et du 100g.
![]() |
![]() |
Comme fichiers j’ai préparé des logos Raspberry Pi (bin oui). Pour les logos Raspberry Pi j’ai utilisé le cutter rotatif fourni avec la machine. J’ai testé plusieurs réglages, finalement j’ai réglé la lame pratiquement contre le cercle du cutter.
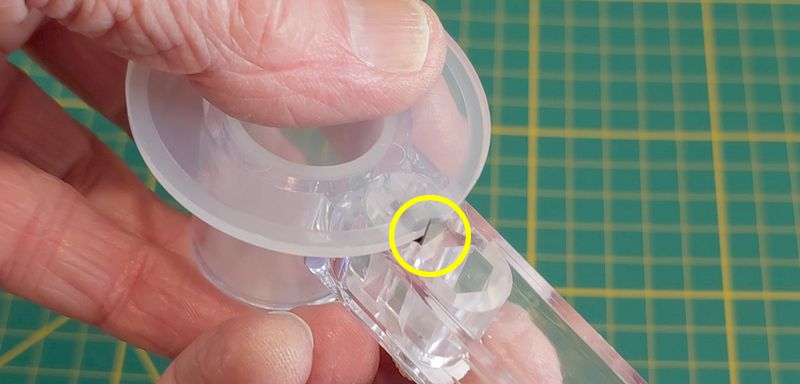
La lame du cutter rotatif. Finalement ce n’est qu’un morceau de lame sécable d’un cutter classique. Il y a plusieurs morceaux de lame, je n’ai pas encore essayé mais je pense qu’avec une lame de 9mm ça va faire l’affaire…
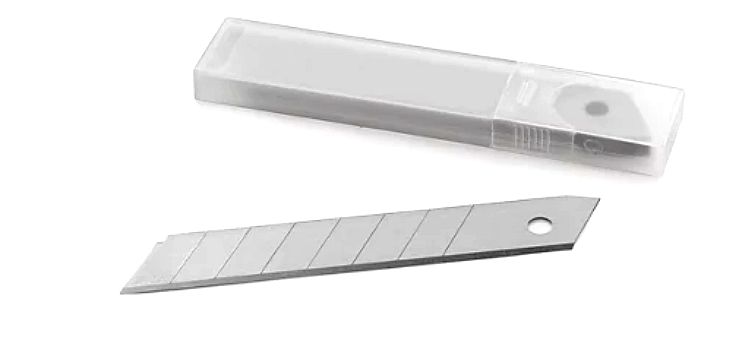
Lame de cutter de 9mm
Avec la molette (flèche bleue) on peut libérer la glissière porte-lame et la faire coulisser (flèche jaune) pour régler à la distance voulue. Dans mon cas pour 54mm de diamètre, je règle au bord du cercle central.
Ensuite on appuie bien sur l’axe central et on fait tourner le bras du cutter autour de l’axe. Pas la peine d’appuyer trop fort, la lame coupe bien.
En final on obtient un cercle de 54mm de diamètre. J’ai réglé le logo pour que sa plus grande dimension soit 39mm et qu’il soit centré.
Pour des CM1 qu’on accompagne avec le FabLab pour découvrir la robotique, je leur ai fait des badges de pilote de Robot mBot. Je pense que ça va leur faire plaisir…
J’utilise Inkscape pour créer les visuels qui garniront les badges. Pour le Raspberry Pi il n’y a pas de cercle autour du logo et je centre pifométriquement le cercle du cutter. Ici j’ai dessiné un cercle de 54mm qui est découpé aux ciseaux. La prochaine étape sera l’automatisation de la découpe avec la machine VEVOR (découpeuse vinyle KH375) dont je vous ai parlé précédemment.
Fabrication d’un badge
Un badge réussi
On peut passer à la phase pratique de fabrication de badge.
Poser une coupelle en métal dans le moule de gauche. elle rentre parfaitement dans la rainure prévue à cet effet.
Poser dessus le papier qui a été découpé à 54mm. Pour un résultat correct, il faut bien centrer le papier pour qu’il y ait un trou identique tout autour du papier.
Poser dessus la feuille de protection en plastique transparent. Attention quand on met la feuille, soit avec l’électricité statique, soit avec le frottement, on déplace le papier avec l’image. Bien veiller à recentrer le tout.
Pousser la glissière sous la presse et poser une coupelle en plastique dans le moule de droite. L’épingle est dessous et le ressort est visible.
Appuyer régulièrement sur la presse jusqu’en butée. Les pions métalliques ne sortent pas des trous dans cette première phase.
Quand vous relevez la poignée, la coupelle, le papier et la feuille de plastique ont disparu ! (flèche jaune). Pas de panique, tout est stocké dans le moule supérieur. Glissez le moule de droite sous la presse.
Appuyez de nouveau sur la presse. Bien à fond. Cette fois les pions vont sortir par les trous et la presse va terminer le sertissage du badge.
Relevez la poignée (elle revient toute seule en position) et déplacez la glissière vers la droite. Le badge est prêt.
On voit d’un coup d’œil si tout s’est bien passé. Ici on peut voir la régularité du sertissage périphérique.
La finition côté image est parfaite également, le film est bien tendu sur le papier.
Un autre badge réussi
Celui-ci c’est pour les petits pilotes de mBot. Le moule de gauche reçoit la coupelle métallique, le papier imprimé et enfin le film transparent.
La coupelle plastique avec l’épingle est placée dans la coupelle de droite.
Après pressage on récupère un badge de « Pilote de ROBOT » !
Le sertissage est parfait
Et la face avant est également tout à fait belle.
On est parti pour équiper toute la classe avec les badges… (25 !)
Avant d’arriver à ce résultat, j’ai fait quelques tests négatifs mais comme dans toute activité manuelle il y a un coup de main à prendre. Les tests ratés font partie du processus… On appelle ça aussi l’apprentissage par essai-erreur.
Un badge raté ?
Pour tout vous dire, j’ai commencé les tests avec du papier Action vendu en carnets. Le papier est assez épais (trop) et le résultat n’a pas été à la hauteur de mes espérances…
Dans un premier temps le papier Action est placé dans le moule de gauche, puis on continue la fabrication et…
On n’est pas loin de la réussite mais comme le papier est un peu trop épais le film n’a pas été serti correctement.
Je n’ai pas rencontré ce problème avec les feuilles de papier en 80g ou 100g.
Après tu as le gars qui ne fait pas attention et monte 2 coupelles métalliques dans le moule
Forcément quand tu presse ça coince ! Le moule est vraiment prévu pour une seule coupelle
😀 . Bon, j’aurais pu dire que c’était pour tester la machine mais non, c’était une connerie bêtise
Du coup le film a été abimé également. Avec les premiers badges mal sertis ça a été mes ratés d’apprentissage !
Vidéo
Conclusion
Comme je le disais au début de cet article, ce genre de machine permet de créer une activité dans un FabLab ou une association. On peut aborder le dessin des badges avec un outil comme Inkscape, passer à l’impression et aux différents paramètres et réglages, types de papiers… Enfin on a des consignes et une procédure à respecter pour aboutir à un résultat satisfaisant.
Au final tout une suite d’acquisitions qui se termine par la production d’un objet que le participant peut emmener, vu son prix.
Cette machine VEVOR est rassurante par son poids et sa solidité, les résultats qu’elle permet d’obtenir sont vraiment réguliers et reproductibles, une fois la phase d’apprentissage (courte) dépassée. Pour la fabrication des badges en 44mm vous pouvez l’obtenir pour 126,99€ avec 1000 badges. De plus le code VVGDS5 permet d’obtenir 5 % de réduction.
Existe également en 25mm, 32mm, 44mm, 58mm, 75mm avec 500 ou 1000 badges.
Sources
Vevor France : https://s.vevor.
Vevor pour l’Europe : https://s.vevor.com/
Ping : Presse à badges VEVOR
Bonjour / bonsoir,
Vous indiquez que l’on peut faire des miroirs, aimants, décapsuleurs, etc…
Mais où les trouvez-vous ?
J’avais questionné Vevor mais ils n’en proposent pas et ils m’ont indiqué que ceux que l’on trouve chez Aliexpress par exemple ne fonctionneront pas avec les matrices fournies avec leurs presses…
Je reste donc à ce jour bloqué à ce niveau là… Si vous avez une piste pour trouver ces éléments qui fonctionneront avec les matrices Vevor, je suis preneur.
Merci
A une époque il y en avait chez Vevor. JE n’ai pas essayé celles de Aliexpress
désolé
cdt
francois
Ils ont dû arrêter la production alors car il n’y en a pas actuellement et leur SAV m’a bien confirmé cela.
Dommage !
Merci pour votre retour en tout cas.
Bon week-end.